Quality Assurance & Control
What is quality? In manufacturing, you cannot control what you cannot measure, sell what customers don’t want, and make a profit with inadequate capability and poor organization. Therefore, quality includes:
- Conformance to specifications
- Conformance to customer requirements
- Capability and footprint optimization.
When problems arise, therefore, they usually have more than one root cause. You have to examine every link in the plan-make-buy-move supply chain. Problems with quality may have originated in planning with understand the customer requirements, in engineering with defining the specifications, in procurement with meeting the specifications, and in any other combination of functions. The use of technology and systems for managing suppliers, capability, footprint, and complexity give you more control of quality and the ability to identify and fix variances quickly.
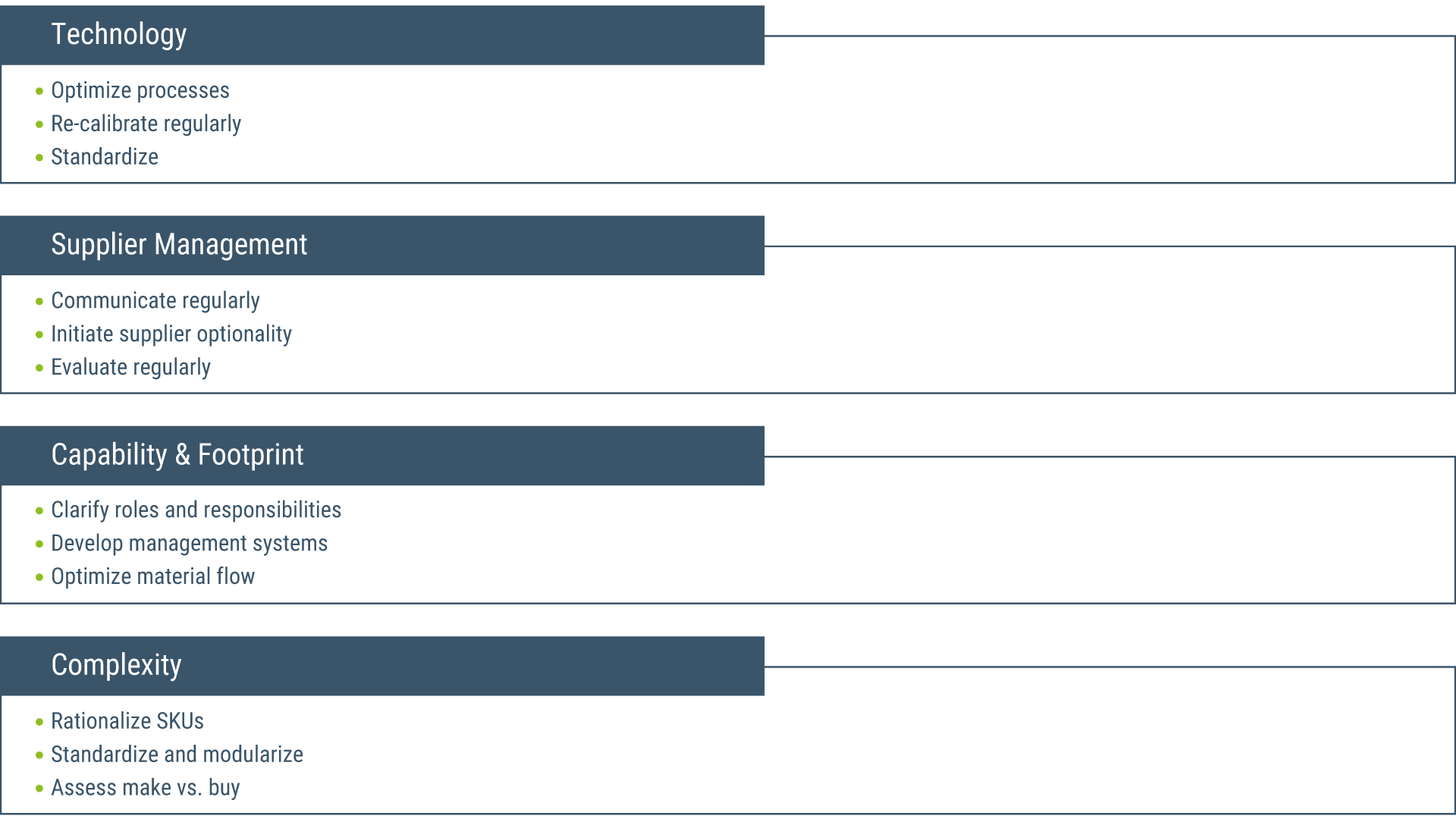
Use technology
Technology for quality control range from individual sensors through machine learning, advanced analytics, and scenario modeling. Technology is most successful when:
- Processes are already optimized.
- Planning, procurement, manufacturing, engineering, and logistics communicate often and clearly.
- KPIs are in space.
- Design, product, and program excellence are in place.
- Suppliers are kept informed and are well managed.
- Owner, responsible, consult, and inform (ORCI) roles and responsibilities are clear to everyone
- A single source of truth has been established, building trustworthy data.
No matter how mechanized your production becomes, errors still occur. Equipment requires regular maintenance and recalibration to keep to requirements. Quality control should be built into each stage of the process, rather than waiting for the end.
Manage suppliers
Collaboration with suppliers is necessary for achieving and maintaining quality. By communicating requirements clearly and meeting regularly, you give suppliers an opportunity to support your quality control efforts, including helping you to comply with regulations.
A manufacturer of consumer products blamed their supplier for quality issues. However, they expected their suppliers to duplicate what the company needed from physical samples only, without any specifications. Once the suppliers received 3D scans and detailed technical specifications, both quality and EBITDA improved.
Supplier evaluations should be scheduled periodically, covering the supplier’s:
- Quality control and assurance management systems
- Ability to handle special orders
- Changes in performance and needs
- Collaboration on delivering higher quality or more compliant raw materials or products.
Manage capability and footprint
The capability of the workforce depends in large part on adequate training, quality management systems, and efficient material flow. Without the right skills, systems, and flow, employees struggle to reach and maintain quality standards.
The customers of a die casting and machinery company were so upset at the number of rejects they received that they insisted on a third-party inspection before products left the company.
An on-site analysis revealed many problems related to capacity, capability, and footprint optimization, including:
- Overworked employees who were unable to maintain both pace and quality
- Inefficient layout of machines and parts causing unnecessary movement and clutter
- Quality inspections only at the end of the process leading to escalating waste
- Poor scheduling of materials, maintenance, and supervision.
The way out of these quality issues included 37 opportunities for improvement, ranging from cross-training to developing a process map for efficient material flow and scheduling. When changes were instituted, the company achieved a 50% to 120% increase in productivity and $1.7 million in annualized savings. Quality improved to the point where the third-party inspection was no longer needed.
Manage complexity
Complexity management encompasses standardization and modularization, analyzing make vs. buy decisions, and establishing feedback loops with customers. Reducing complexity increases efficiency and reduces errors. Rationalizing SKUs, for example, simplifies procurement, operations, and logistics.
The more complex the supply chain, the more difficult it is to gain visibility into the exact causes of quality problems. When complexity is managed, you not only improve quality assurance and management, you also have greater insight into spend and performance and a greater likelihood that you can quickly resolve variances quickly.
Quality is not the result of just one function doing its job; it depends on coordination across the plan-make-buy-move supply chain. If you wish to improve quality and reduce variances, then the right technology and the right management systems, coupled with visibility into the supply chain, will help you meet your goal.
Related Resources
Ready to improve your consumer demand forecasting?
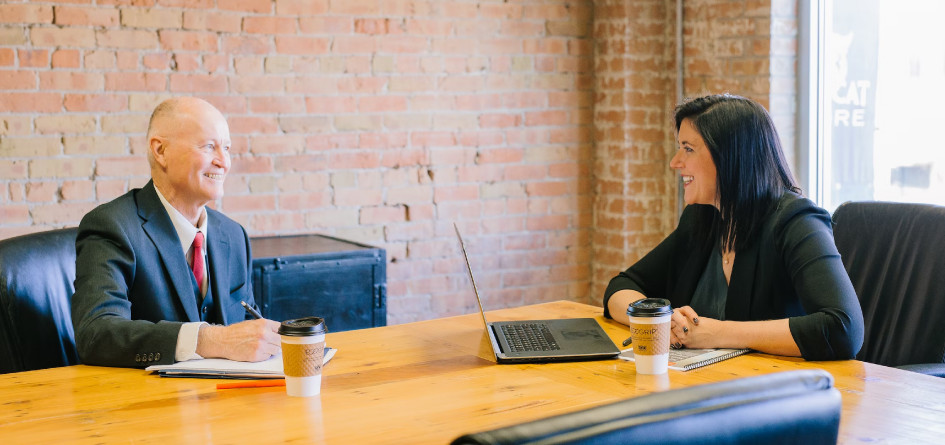
Talk to us
From rapid sprints for short-term gains to transformation for competitive advantage we are here to get you there.
Schedule a discussion
Submit this form to speak to an SGS Maine Pointe representative.
Prefer a call? (781) 934 - 5569