Footprint optimization
What is the best way for your company to organize its facilities and its assets to get the maximum productivity, efficiency, and quality, including energy efficiency and waste management?
An optimized footprint is one where assets are fully utilized, the layout and design are efficient and safe, and sustainability—the carbon footprint—is taken into consideration.
Asset utilization
A company with multiple locations may not realize that equipment is standing idle in one facility or location, while another lacks the equipment it needs to meet demand. Downtime between shifts, poor maintenance, and inefficient processes all contribute to poor asset utilization.
A cable manufacturer ran some of its equipment at 20% below capacity because they went idle at every shift turnover. They also lacked a daily schedule control (DSC) process to answer such questions as: How many feet of cable did manufacturing run through each machine? Did manufacturing produce to goal? With a hot handover and DSC process in place, throughput improved 14% with a $3 million to $5 million incremental profit.
Asset utilization may be calculated in several ways. Product yield compares the total number of good units produced to the total number expected. OEE calculates losses due to poor quality plus non-availability plus slow running. Planned versus unplanned downtime and maintenance costs vs. cost of goods sold (COGS) my pinpoint problems with maintenance or the equipment itself.
To improve the utilization of assets, you must evaluate, among other factors:
- Downtime
- Shift handovers
- Maintenance scheduling
- Supply/demand balance
- Labor shortages
- Labor capability
- Product and brand mixes
- Owner, responsible, consult, and inform (ORCI) roles.
Layout and Design
By streamlining processes and eliminating wasted motion, time, and materials, companies create a more productive workplace. In one case, reorganizing a single function in a plant meant more could be done with fewer people. The people who were no longer needed were reassigned to areas where labor was in short supply.
An optimum layout and design means that equipment and people are in the right place at the right time. For example, a contractor’s dozers stood idle waiting for spare parts because no one had clear responsibility or a standard method for re-ordering vulnerable parts ahead of time.
Achieving an optimum layout and design requires:
- Standardized processes
- Integration of automation
- Predictive maintenance
- Safety
- Employee training
- Clarity of roles, including owner, responsible, consult, and inform (ORCI)
- Lean, 5S, and similar strategies.
Sustainability
A reduced carbon footprint is essential not only for compliance with the Greenhouse Gas Protocol but also for more efficient and cost-effective operation. By reducing the use of energy, water, and waste, companies reduce expenses and pursue design to value goals that give them a competitive advantage.
To improve footprint design, you must evaluate, among other factors:
- Energy efficiency
- Waste reduction
- Process optimization
- Water conservation
- Emissions control
- Alternative, sustainable raw materials
- Green technology.
Related Resources
Ready to take hold of your supplier performance management?
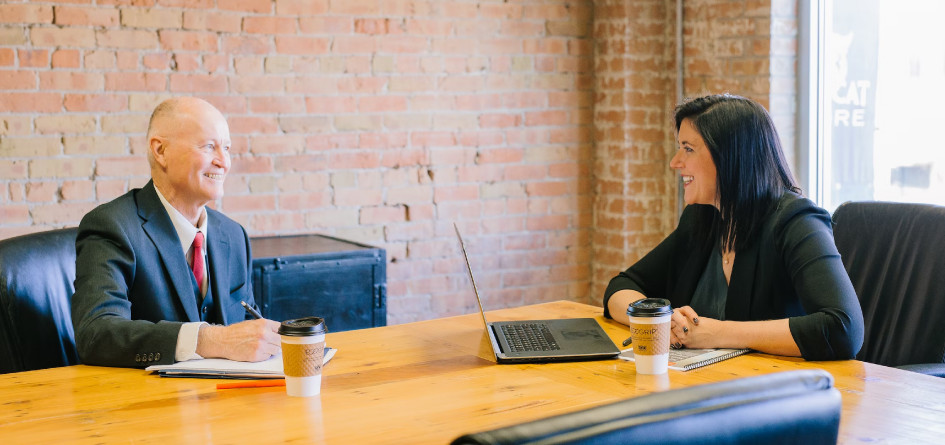
Talk to us
From rapid sprints for short-term gains to transformation for competitive advantage we are here to get you there.
Schedule a discussion
Submit this form to speak to an SGS Maine Pointe representative.
Prefer a call? (781) 934 - 5569